
трехмерная печать
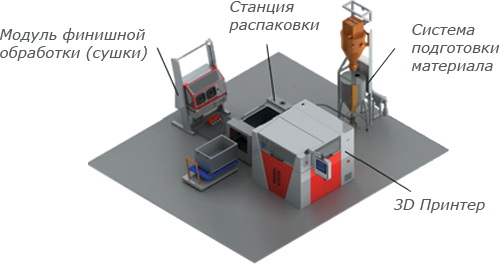
Трёхмерная печать
Мы живем в эпоху, определяемую многими как третья промышленная революция. Трехмерная печать, которую на профессиональном языке следует называть аддитивным производством, уводит нас с позиций эры линий массового производства и приближает к новой реальности производства, удовлетворяющей требованиям заказчика, – одноразовой продукции.
Нужна запасная часть для ремонта оборудования? Как это происходит сейчас: вы обращаетесь в вашу сервисную службу, которая получает запчасть от дистрибьютора, который, в свою очередь, размещает заказ у производителя, где эти запчасти массово производятся на дорогостоящем оборудовании. В будущем вы просто распечатаете нужную деталь на вашем 3D принтере из скачанного файла данных САПР. Если у вас нет подходящего принтера, можно будет просто распечатать её на каком-нибудь из местных производств.
Voxeljet – ваш партнер для
современного производства
Компания Voxeljet – мировой высокотехнологичный производитель систем 3D-печати, предназначенных для промышленного применения. Также компания является одним из крупнейших центров в Европе по производству форм и моделей для литья металлов.
Бизнес-подразделение Voxeljet Systems специализируется на разработке, производстве и установке систем 3D-печати. Именно здесь создаётся продукция, в которой воплощаются инновации, скорость и высокая производительность. Сегодня voxeljet имеет широчайший ассортимент продукции, который включает как небольшие, так и крупногабаритные модели машин. Это позволяет компании предлагать системы 3D-печати практически для всех областей промышленности.
Комания Voxeljet Services внедрила самый современный сервис центр по созданию песчаных форм и пластиковых моделей. Опираясь на полученные от заказчиков CAD-данные с использованием процесса 3D-печати, изделия производятся максимально быстро и эффективно. Клиентская база компании включает широко известных производителей автомобилей и их поставщиков, а также инновационные компании из области искусства и индустрии дизайна.


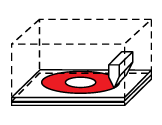

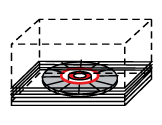



Изделие создаётся слой за слоем. Для этого процесса необходимы 3D-CAD-данные, которые передаются через STL интерфейс для запуска процесса подготовки программного обеспечения. Далее цифровая модель разбивается на отдельные слои. Формы помещают в рабочую зону, где и начинается процесс. Базовый материал равномерно наносится на всю ширину сборки. Печатающая головка со связующим веществом используется на тех участках, где модель будет производиться, связующее вещество проникает в нанесённый последним слой и связывает его с нижним слоем. Конструкция платформы опускается, и процесс повторяется снова. После завершения формирования оставшийся материал удаляется вручную. По окончании процесса пресс-формыочищаются. Они могут быть смонтированы и подготовлены для литья. При литье в песчаные формы форма выступает в качестве негатива для процесса литья.
- Может использоваться для прототипирования,
функциональных моделей или разрушаемых моделей. - Точное наслоение и высокая точность
- Компоненты высокой сложности
- Пропитывание любым цветом
- Идеально подходит для прецизионного литья, т.к.
основной материал – ПММ - Экономически выгодное производство как партии
с одним размером, так и серийного производства - Быстрая доставка в течение нескольких рабочих дней.
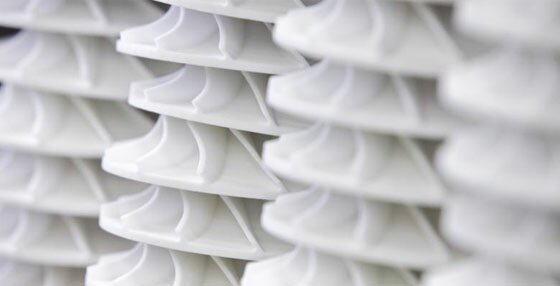
- 100% неорганическое связующее вещество;
- хорошая прочность на изгиб;
- подходит для литья для всех распространённых
сплавов; - низкий уровень выбросов во время литья;
- низкие эксплуатационные расходы;
- процесс протекает при комнатной температуре;
- песчаная смесь поставляется готовой для
использования.
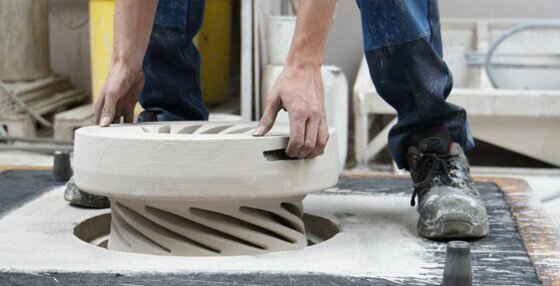
